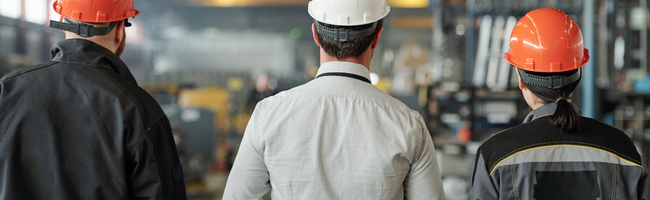
Integration at process level
A cascade system using isobutane and isopentane is integrated in a protein drying.
The first of the two high-temperature heat pump systems developed in the project will be integrated in a protein drying. The system is a cascade system using hydrocarbons (isobutane and isopentane) and semi-hermetic commercial compressors from Frascold for supply temperatures of up to 150 °C.
Modification and optimization of compressors
The compressors will be modified and optimized for high-temperature applications, leveraging the compressor portfolio to higher supply temperatures, and thereby making a variety of technologies available for high-temperature applications. The development of the semi-hermetic screw compressors in this project will leverage the results from the SuPrHeat project », where similar developments were conducted for semi-hermetic piston compressors.
The sudden change in capacity on the low or high temperature side poses a challenge when designing the system and making sure that the operation runs smoothly. The low temperature side heat rejection must be in balance with high temperature side. Thus, the cascade system must be designed with a load balancing system and an advanced control system.
The system will be designed for a heat supply capacity of 300 kW to 500 kW (depending on the supply temperatures up to 140 °C), while the final application range will cover capacities from 500 kW to 1500 kW. The protein dryer is working with a capacity up to 550 kW, where steam heat exchangers are installed in the dryer and are heating up the drying air in direct contact.
Demonstration principle at process level
The principle behind the demonstration at process level is that the moist air coming out of the dryer becomes the source for the heat pump. The surface temperature of the evaporator is below the dewpoint of the air, and the moisture condenses on the surface of the evaporator. The heat evaporates the refrigerant, and the refrigerant is compressed to a higher pressure and temperature in a compressor. The refrigerant condenses and rejects the heat from the evaporator and compressor in a condenser and heat up the air, which is coming into the dryer. An existing natural gas heater is kept as backup for the heat pump demonstration.
Overview of heat pump integration at process level.
Reevaluation and optimal compromise
The integration will include a reevaluation of the main process parameters of the production of the protein powder to find the optimal compromise between the heat pump performance and the product quality as well as the throughput of the dryer.
The main developments of the system includes:
- High-temperature heat pump system specifically for drying of protein powder
- Semi-hermetic commercial compressors from Frascold
- System by Multi Køl & Energi
- Demonstration capacity: 300-500 kW
- Application capacity: 500 kW to 1500 kW
- Simultaneous process and heat pump optimization