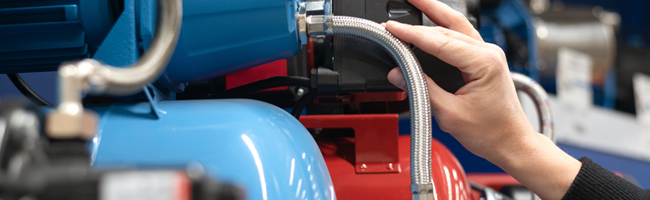
Compressor technologies
Three different compressor technologies are relevant for high-temperature heat pump applications.
Applications with high or low temperature lift
Industrial heat pumps recover heat from a low temperature heat source and upgrade it to higher, useful temperatures where it is supplied to a heat sink such as process heat. To upgrade the heat, electricity is invested, while the amount of electricity to be added is dependent on the temperature lift: higher temperature lifts require a larger amount of electricity. The ratio between the required electricity and the supplied heat is called “Coefficient of Performance” (COP) and describes the operating performance of the heat pump.
The best performances are accordingly achieved for low temperature lifts. This phenomenon causes that most installed systems can be found in applications with low temperature lifts. In these applications, the obtainable performances were good enough to overcome the typical barriers associated with the integration of heat pumps.
Competitive solutions
Various new systems, especially for supply of district heating, were installed during the recent years, and for supply temperatures below 90 °C, ammonia systems have proven to be especially competitive.
However, several factors are moving in a direction, where industrial heat pump-based solutions become more competitive. These factors include the following:
- A decreasing ratio between the electricity cost to operate the heat pump and the fuel cost for the alternative combustion-based process heat supply
- An increasing focus on CO2 emissions from process heat supply and a higher awareness of environmental benefits of heat pump-based process heat supply
- A higher awareness of energy efficiency in industrial processes and a willingness to exploit excess heat
- Technological advancements in the development of high-temperature heat pumps.
These aspects cause industrial heat pumps to become competitive alternatives, even in applications with high temperature lifts and accordingly high supply temperatures. Thus, industrial heat pumps are becoming the technology, which is expected to have the most optimal performances in terms of energy efficiency, operating expenditures, and life-cycle cost for supply of heat at temperature way above 100 °C.
High-temperature heat pump technologies
Overviews on the state-of-the-art of high-temperature heat pumps show that the availability of systems suitable of supply temperatures above 100 °C is limited and insufficient when considering the large demand for such systems. Developing systems for higher supply temperatures requires the optimization and modification of the systems and most of its components, while the compressor is the most important part.
In connection with compressor developments, three main approaches for enabling higher temperatures can be observed.
Compressors from process industries
Compressors for process industries are readily available and could be used for heat pump systems. These compressors are, however, expensive and only competitive for heat supply capacities above 15-20 MW, and they have only limited experience from high-temperature heat pump applications.
Modified refrigeration compressors
The operating range of compressors from refrigeration industries is continuously being adapted to become suitable of higher supply temperatures. This is the most promising option for developing cost-effective, high-performance equipment, which can be available in large volumes in close future. Commercial compressors are available within the range of 50 kW to 1000 kW and industrial compressors are available within the range of 1 MW to 15 MW.
Novel and strongly adapted technologies
These technologies are based on novel approaches or adapted from other applications. These comprise Sterling heat pumps, turbocompressors from sport-cars, piston compressors based on truck engines or spindle compressors based on vacuum pumps.
These technologies are mostly in the prototype stage with only a few single demonstrations. The approaches based on automobile technologies aim for mass-produced equipment and have the potential of becoming very cost-effective. Thus, they have a large potential, while the spindle compressor is expected to have outstanding technical performances. Some technology can reach high temperatures, but has a limited efficiency and considerably higher investment cost (e.g. four to five times compared to refrigeration compressors).
Relevance of development approaches
The three compressor development approaches are all relevant due to specific aspects. The large process industries compressors are aiming for the large-scale applications to benefit from economy of scale.
The novel and strongly adapted technologies have promising market perspectives as they are based on technologies which benefit from either expected high performances, technical features enabling high temperatures, low cost, or a combination of all three.
The modified refrigeration compressors are the most promising approach when aiming for technologies which can cover large market shares and be produced in large volumes.
For these technologies, supply chains and service and maintenance networks are established and could be adapted to high-temperature applications.